How Cut and Sew Manufacturers Use Pattern Grading for Full-range Clothing?
- Lydia Design Studio
- Nov 15, 2024
- 5 min read

Pattern grading was first executed in the fashion industry during the commercial boom in the 19th century. This approach was developed to facilitate the mass production of garments.
It saves pattern makers from the tedious task of recreating various patterns for a single design. This method has proven so effective that cut-and-sew manufacturers and pattern-makers depend on it to produce patterns in a full-size range for any fashion collection.
Usually, pattern makers start with a mid-size pattern and then adjust it up or down without changing the initial design.
Grading is an art that can significantly benefit pattern makers, saving a lot of resources and time. In this blog post, we’ll discuss pattern grading and commonly used techniques to generate a complete size range for any design.
What is Pattern Grading?

The procedure of crafting patterns in different sizes from a base pattern by using a specific size chart is referred to as pattern grading. When designing a garment for ready-to-wear clothing in various sizes, apparel manufacturers often use grading as a method.
Garment grading is the practice of manually or digitally modifying your sample pattern from one size to another using a size specification chart. However, the style, appearance, or shape remains intact. The smallest or medium size typically serves as the starting point.
Although the overall shape and appearance of a design remain the same, grading rules are adjusted according to the size of the design.
Understanding the Basics: Grade Specs and Grade Rules
Grading specifications, commonly referred to as "grading specs," are indicators that illustrate how much you want each size to expand or contract. They essentially convey the same information to the manufacturers as your pattern grading guidelines do.
The grading rule specifies how much each point of measurement (POM) is adjusted in size to accommodate a broad range of sizes. Its primary aim is to ensure that the garment fits properly and maintains a balanced silhouette.
How to Develop Grading Guidelines and Specs?
The approach you take for determining a grade largely depends on the type of style being produced. If you're designing athletic wear, the size patterns should allow sufficient space for movement. For a boxy-shaped design, each size must incorporate additional room for an oversized fit.
Before establishing grading specifications, you must measure the sample size. Some of these measurements will be derived directly from your body dimensions, while others will be influenced by your body measurements along with the garment's ease.
Some basic points of measurement include:
Full garment length
Chest
Waist
Hip
Sleeve length
Neck width
Front neck drop
Across shoulder
After tallying all points of measurement, you can apply the grading rule to determine which sizes are larger or smaller based on the sample size you selected.
Grading Techniques Used by Cut and Sew Manufacturers
There are two basic grading techniques:
Traditional Pattern Grading
Digital Pattern Grading
Traditional Pattern Grading
Patterns can be resized manually by shifting the pieces by a specific distance to generate new sizes. This can be achieved through techniques like the slash and spread method or pattern shifting.
Slash and Spread Method
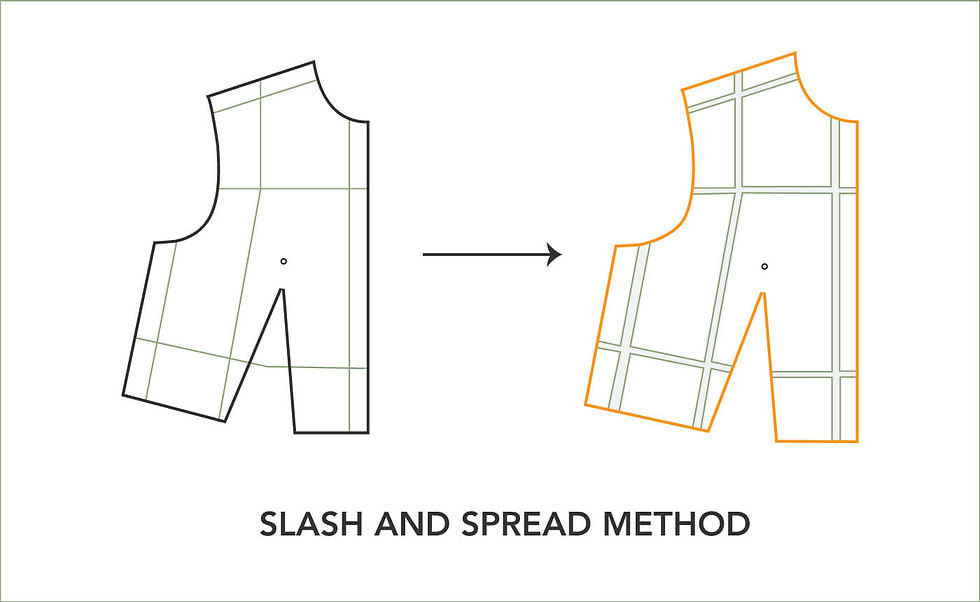
The slash and spread technique entails cutting the pattern at designated cut lines and either spreading or overlapping the sections to produce larger or smaller sizes. Depending on the shape, pattern makers must decide strategically where to cut, ensuring that all parts of the garment are graded without being distorted.
Pattern Shifting Method
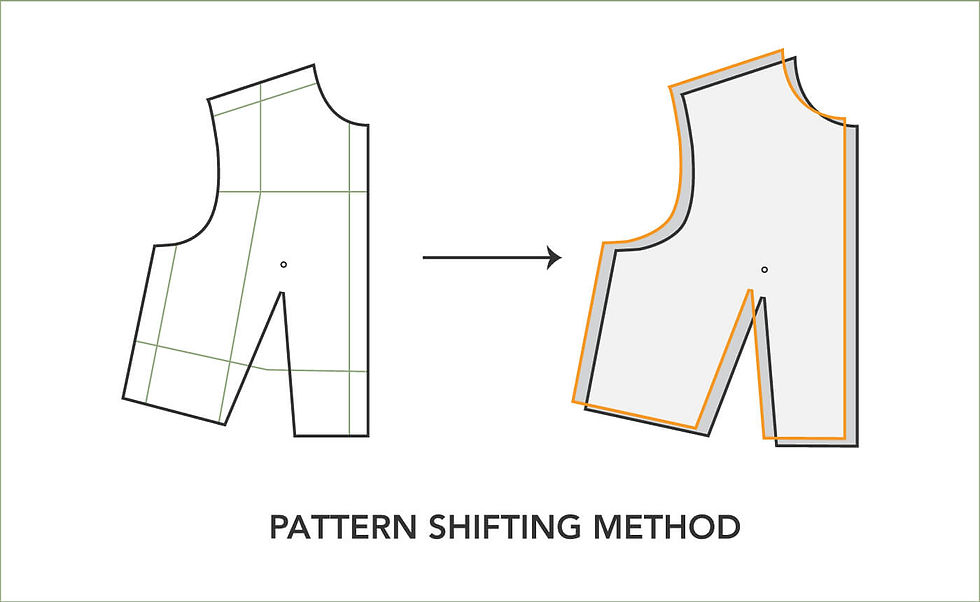
Pattern shifting is another manual grading approach where the pattern is traced and adjusted up, down, left, or right by a fixed distance to generate new sizes. This method is somewhat similar to the slash and spread technique.
While the slash and spread method involves cutting the pattern into segments, pattern shifting keeps the pattern whole, which is the primary distinction between these two grading techniques. To create smaller sizes, the pattern is moved inward from a certain point, and vice versa.
Digital Pattern Grading

Digital grading is the preferred technique for mass production within the fashion industry. By utilizing digital pattern-making software, you can automatically modify your pattern sizes based on predefined rules, significantly saving time and effort.
Dimensional Grading — Computer-aided Pattern Grading
The fastest method for pattern grading is computed grading (CAD). With this process, manufacturers can rapidly achieve patterns that are more accurate, precise, and detailed. Today, the cost of CAD software has become more affordable, making it an accessible choice to fashion experts.
This method has progressed alongside advancements in modern fashion technologies. It is considered the quickest approach which digitizes techniques such as “splash and spread” and “pattern shifting” using a similar process.
Computer-based grading systems operate in two modes:
The grading increments are input into the computer, which then automatically produces various sizes using the same methods as manual grading.
Starting with data from size specification charts, the pattern for each individual size is calculated separately.
What are Different Grading Practices?
Various types of grading are employed in the clothing design process. Below are the most effective and commonly used ones.
Creating Flat Patterns

This process requires crafting a basic, fitted pattern that comfortably fits a person or body shape. It’s a straightforward pattern that permits comfortable and unrestricted body movement.
Women’s clothing typically consists of five essential pattern pieces: a basic neckline, a sleeve, a fitted skirt featuring darts on both the front and back, and a form-fitting bodice for the front and back. By altering these fundamentals, various styles can be created.
Since a basic pattern lacks seam allowances, it simplifies the process of adapting it into different styles.
Drafting

Design patterns or basic design elements are produced through drafting. For that, measurements derived from sizing charts or precise measurements taken from a person, garment, or body form are utilized in this process.
These measurements for the chest, waist, hips, and other body areas are marked on paper. After that, the construction lines are drawn to complete the pattern.
Draping
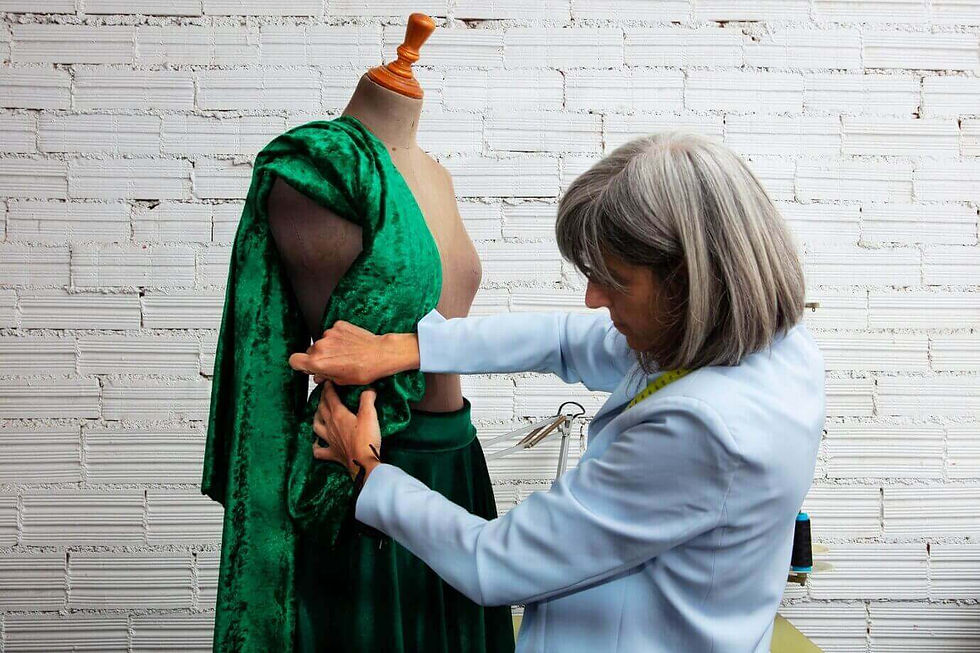
A piece of fabric is positioned around a form and adjusted to its shape to create a three-dimensional fabric pattern. To ensure the garment is comfortable to wear, ease of movement allowances are incorporated.
One advantage of draping is that it allows the designer to visualize the overall design effect of the finished garment on the body form before cutting and sewing any garment pieces.
However, this method is more expensive and time-consuming than creating flat patterns. Draping can be done on either a human body or a mannequin.
Conclusion
Pattern grading is a highly beneficial method that helps pattern-makers create garments that fit well to a range of body shapes and sizes. While grading guidelines may vary depending on the final design or the type of fabric, they consistently promote inclusivity and adaptability in clothing lines.
Accurately drafted patterns according to your measurements and utilizing software help eliminate much of the fitting trial and error in the sewing process. This also ensures that your fashion collections serve a diverse range of clients in different sizes.
Commentaires