CMT Production: Benefits and Challenges in the Apparel Industry
- Lydia Design Studio
- Jan 6
- 4 min read
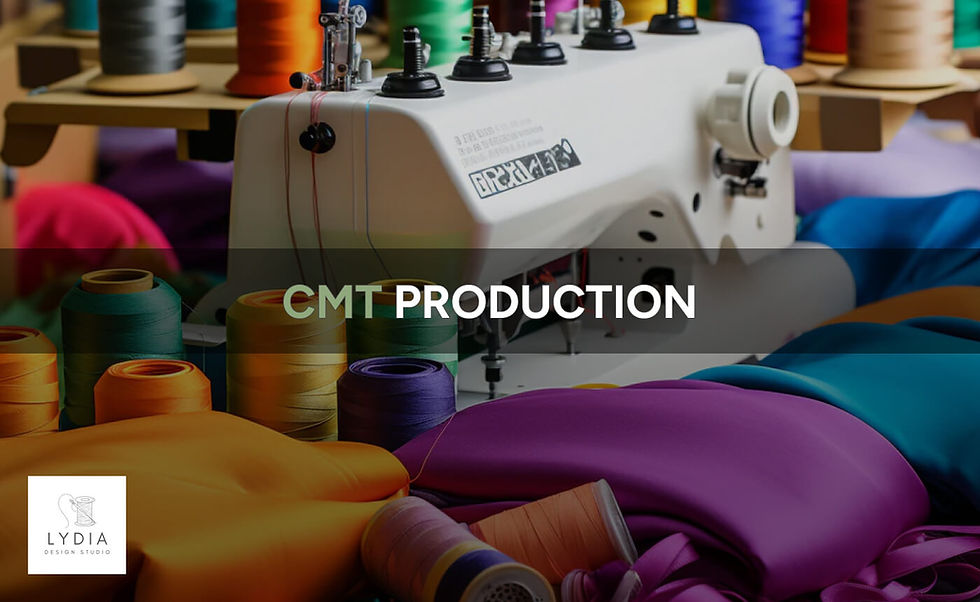
The initial stages of production and product development are critical when starting a fashion apparel line. There are two main production options available for efficiently manufacturing your apparel collection:
FPP (Full Package Production)
CMT (Cut, Make, Trim)
FPP clothing production encompasses the entire manufacturing process, including design, fabric sourcing, pattern making, sewing, quality control, packaging, and delivery.
In contrast, CMT focuses on fabric cutting and manufacturing, resulting in the final product.
Each production model has its own unique processes, market challenges, and notable advantages and disadvantages. Considering these factors, brand owners can choose the option that best fits their brand's aesthetics and budget.
This blog post will provide a comprehensive overview of CMT clothing production, including its definition, process, and the pros and cons associated with it in the apparel industry.
Let’s dive in!
What is CMT Manufacturing?
CMT manufacturing refers to a production method where the clothing manufacturer offers only the cutting and sewing services, while the brand supplies the fabric and essential techpack.
This production method allows the brand to maintain full control over the quality and selection of materials used in the production phase.
CMT Manufacturing: The Process
Phase 1: Cut
The initial phase of CMT production is pattern cutting. The fabric is cut according to the patterns and grading provided by the brand. Clothing manufacturers typically employ specialized machines and advanced cut-and-sew techniques to achieve precise cuts, ensuring high-quality results.
Manufacturers adhere to the specifications brands provide at this stage, so it’s essential to give accurate information.
Important Steps in the Cutting Process
Fabric Spreading: Firstly, the fabric is arranged in layers to facilitate cutting multiple pieces simultaneously for maximum efficiency, material conservation, and production speed.
Marking and Cutting: Next, the paper patterns are placed over the fabric layers, and expert craftsmen use specialized markers to indicate cutting lines. After accurate cutting lines are identified, sharp tools like rotary cutters or electric fabric cutters are employed to execute the cutting.
Identifying Parts: Each cut piece is labeled or tagged to ensure proper identification and organization of the various pieces for later stitching.
Quality Control: Throughout the cutting process, quality control measures are implemented to check for defects, maintain consistent dimensions, and confirm that the correct number of pieces has been cut.
Phase 2: Make
Once the fabric is cut, manufacturers proceed to the next stage, which involves assembling the fabric pieces and stitching them together to create the final product. Typically, this is accomplished using machinery to achieve a quick and precise finish.
Important Steps in the Stitching Process
Pattern Placement: The cut fabric pieces are carefully arranged and moved into the stitching line to prevent any interruptions that could disrupt the stitching phase.
Sewing Techniques: Skilled tailors use various sewing methods, such as zigzagging, overlocking, and decorative stitching, to expertly join fabric pieces while ensuring long-lasting durability.
Quality Checks: Ongoing inspections during the stitching process are conducted to identify and correct any sewing imperfections, ensuring the fabric meets necessary quality standards.
Phase 3: Trim
After the garment is stitched, the final touches are applied. This concluding stage also includes a comprehensive quality inspection of the apparel before its final delivery.
Important Steps in the Trimming Process
Garment Fastening: Items such as buttons, snaps, hooks, and zippers are attached to garments using specialized tools or hand-stitching techniques to ensure the closures are secure and operate correctly.
Labeling and Branding: To adequately inform consumers of any care instructions and to maintain brand identity, clothing tags that feature the brand name or logo, as well as care instructions and sizes, are sewn or adhered using heat to each piece of clothing.
Decorative Embellishments: Elements like lace, ribbons, appliques, and embroidery serve as decorative features that enhance the aesthetic appeal of clothing, making them unique and stylish.
Quality Assurance: During the trimming process, it is verified that all embellishments are correctly placed relative to one another and are free from flaws, using quality control methods.
Packaging: After trimming, garments are folded, placed in protective bags, and labeled for shipping to retailers or customers.
Benefits and Limitations of CMT Production
In the apparel manufacturing industry, CMT production offers brands amazing benefits, however, this production avenue does have some drawbacks. Let’s explore them all.
Benefits of CMT in Supply Chain
Focus on Design and Marketing
For brands, hiring CMT clothing manufacturers is a smart way to concentrate on designing and marketing their products while leaving the production to specialists.
Expertise and Efficiency
It allows brands to benefit from skilled professionals who use advanced technologies to efficiently handle tasks like cutting and assembling garments.
Flexibility and Scalability
CMT offers great flexibility in managing production volumes. Brands can adjust their output according to market demands without the constraints of operating a fully-equipped manufacturing facility.
Cost-Effective Production
By outsourcing specific manufacturing processes to specialized individuals, CMT allows clothing brands to lower their costs — avoiding significant expenditures on machinery and labor.
Limitations of CMT in Supply Chain
Communication Challenges
Working with various manufacturers at different stages of production can lead to communication issues, resulting in delays or misunderstandings in the production process.
Dependency on Suppliers
Depending on external suppliers for crucial production stages creates reliance on suppliers’ capabilities and production volume, which can pose risks if the supplier encounters difficulties or delays.
More Time Consumption
Brands need to put more time and effort into connecting with the right vendors for fabric sourcing, ensuring timely deliveries to manufacturers, and managing inventories efficiently. This focus can sometimes lead to the neglect of other crucial business operations.
Final Words
As the fashion industry continues to evolve with advancements in technology and shifting consumer expectations, staying informed about various production methods and their challenges is essential.
By mastering the intricacies of CMT manufacturing, brands can enhance their operational efficiency and deliver products that meet market demands with precision.
Partner with the Best CMT Clothing Manufacturers
Lydia Design Studio is among the leading clothing manufacturers in Atlanta, helping clothing brands build premium collections for their target customers. Along with Full Package Production (FPP) services, we also offer CMT manufacturing for brands seeking to balance creative control with efficient manufacturing.
With our expertise and meticulous attention to detail, we help you bring your designs to life while maintaining top-tier quality. Partner with us to set your clothing brand apart from competitors and elevate your production process to the next level. Book a free consultation today!
Comments